Chez Bugatti, l’incorporation de l’option « carbone apparent » impose au fabricant la fabrication de pièces d’une qualité visuelle impeccable. Cela s’ajoute aux exigences structurelles déjà considérables pour une Chiron.
Deux catégories de pièces en carbone
Aujourd’hui, on peut clairement distinguer deux catégories de pièces en carbone dans le monde : celles qui sont purement esthétiques et celles qui ont un rôle structurant réel dans la solidité d’un produit. Dans le domaine de l’aéronautique, seules les pièces structurelles sont utilisées. Cependant, dans le secteur de l’automobile, on trouve les deux types : des insertions en carbone dans certaines voitures de luxe, qui n’ont qu’une fonction esthétique, et des coques ainsi que des éléments de carrosserie et aérodynamiques qui contribuent à la tenue de route et au maintien global de la structure d’un véhicule.
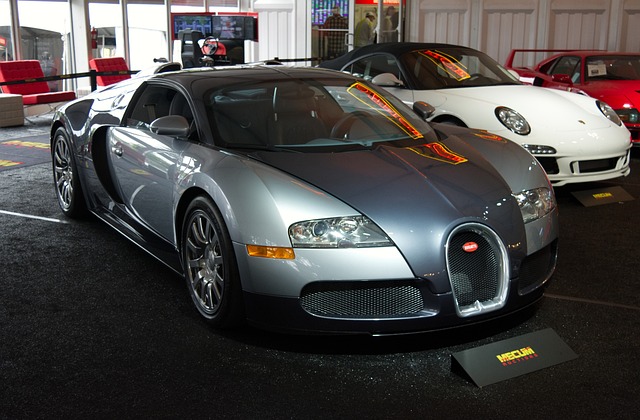
Faire et refaire …
Le client qui souhaite une Bugatti avec une carrosserie « carbone apparent » place donc une demande exigeante qui mettra fortement à contribution les artisans de Bugatti, qui ne peuvent se permettre la moindre erreur. Cependant, il est important de noter que Bugatti n’est pas directement impliqué dans la fabrication du carbone lui-même. Ce domaine est plutôt le territoire de géants tels que Toray, qui probablement fait partie des fournisseurs de ce fabricant de Molsheim.
« L’équipe design requiert que les fibres de carbone soient alignées à un angle de 45°, avec une arête centrale parfaite. Si l’angle dépasse de plus de 1 ou 2 degrés, le panneau devra être refait à partir de zéro. Si des fibres ne sont pas alignées, si le matériau s’effiloche ou s’il présente des bosses ou des plis, le panneau devra également être refait« .
Aujourd’hui, il existe deux méthodes principales pour travailler le carbone. La première, plus complexe et moins courante, est le processus de « tissage » des fibres brutes, similaire à la manière dont on tisse des fils de soie, à l’aide d’une sorte de grand métier à tisser. Une fois que les fibres sont tressées dans la forme souhaitée, de la résine époxy est injectée (par moulage par injection), puis l’ensemble est soumis à une cuisson à des températures dépassant les 100 degrés Celsius pour former la pièce en carbone finale.
L’autre méthode couramment utilisée pour fabriquer des pièces en carbone consiste à utiliser des rouleaux de stratifié pré-imprégné, où la fibre de carbone est déjà mélangée à la résine. On découpe alors les formes souhaitées à partir de ces grands rouleaux, qui sont semblables à des rouleaux de toile cirée que l’on trouve en magasin. Ces formes sont ensuite insérées dans un moule et soumises à un processus de mise sous vide pendant la cuisson dans un autoclave.
Bugatti ne spécifie pas quelle méthode est employée pour la fabrication de ses pièces en carbone. La plus grande de ces pièces mesure plus de deux mètres de long (un panneau latéral) et nécessiterait une semaine entière de travail pour être réalisée.
Un défi majeur associé au carbone demeure son impossibilité presque totale à être réparé en cas de choc ou d’accident. Si la structure en carbone de la Chiron est endommagée lors d’un accident, il est fort probable que l’hypercar soit irréparable. De plus, le carbone est difficile à recycler, car cela nécessiterait de séparer la fibre de la résine, ce qui est une opération complexe.
Voitures d’occasion, Actualités automobiles, Vous aimerez lire aussi …
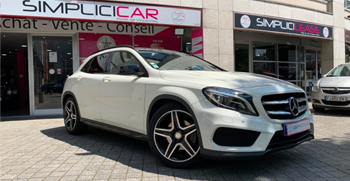
Mercedes GLA finition AMG occasion
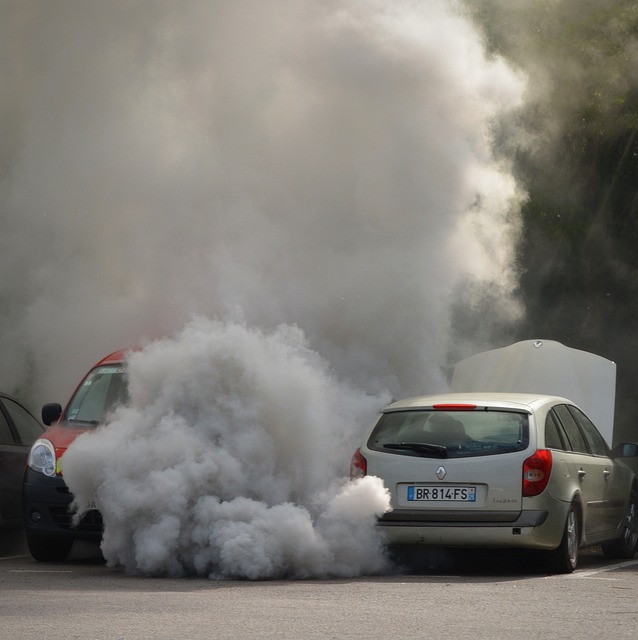
Le délai de prescription pour vice automobile caché passe à 20 ans
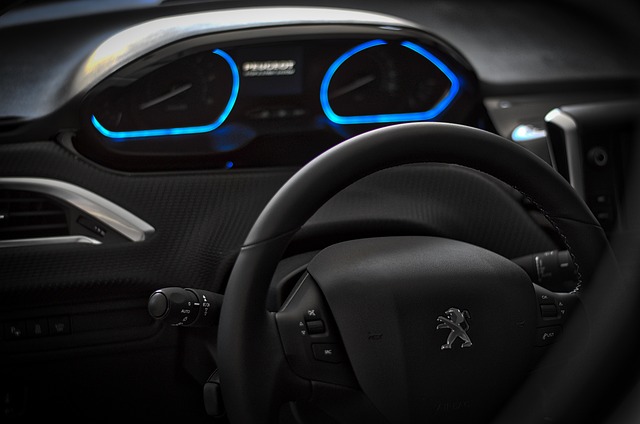
Découvrons la 408X, version chinoise de la Peugeot 408
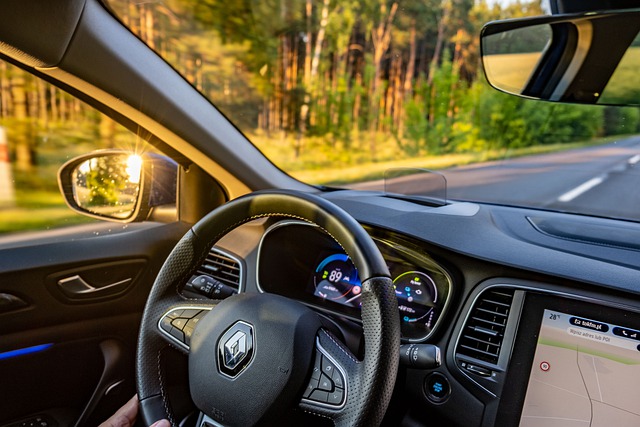
Petit contretemps pour la Renault Mégane E-Tech
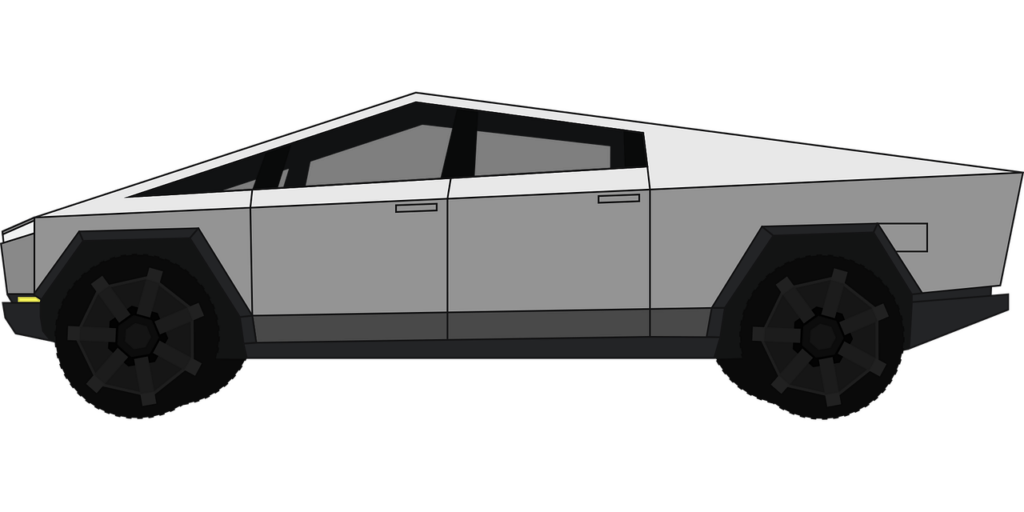
Tesla Cybertruck se déclinera en divers coloris
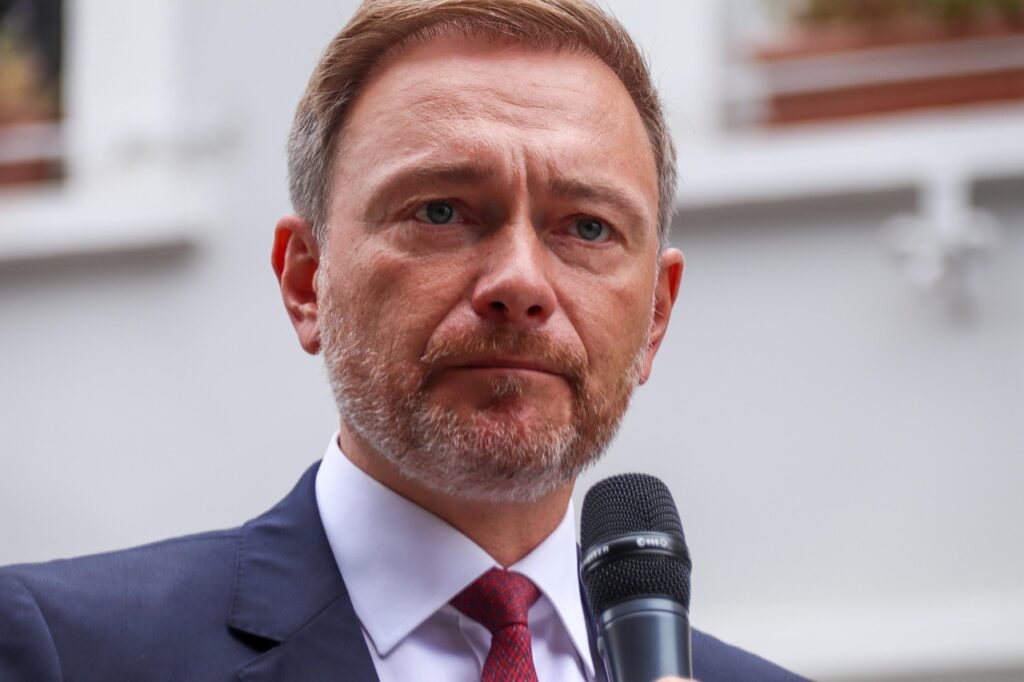